digital Phase Converters: A Comprehensive Guide
A digital phase converter is a sophisticated electronic device that transforms single-phase electrical power into balanced three-phase power. This conversion is crucial for operating three-phase equipment, such as industrial machinery, in locations with limited access to three-phase power supplies. Unlike traditional rotary phase converters, digital models leverage advanced electronics and software to achieve high levels of performance and efficiency.
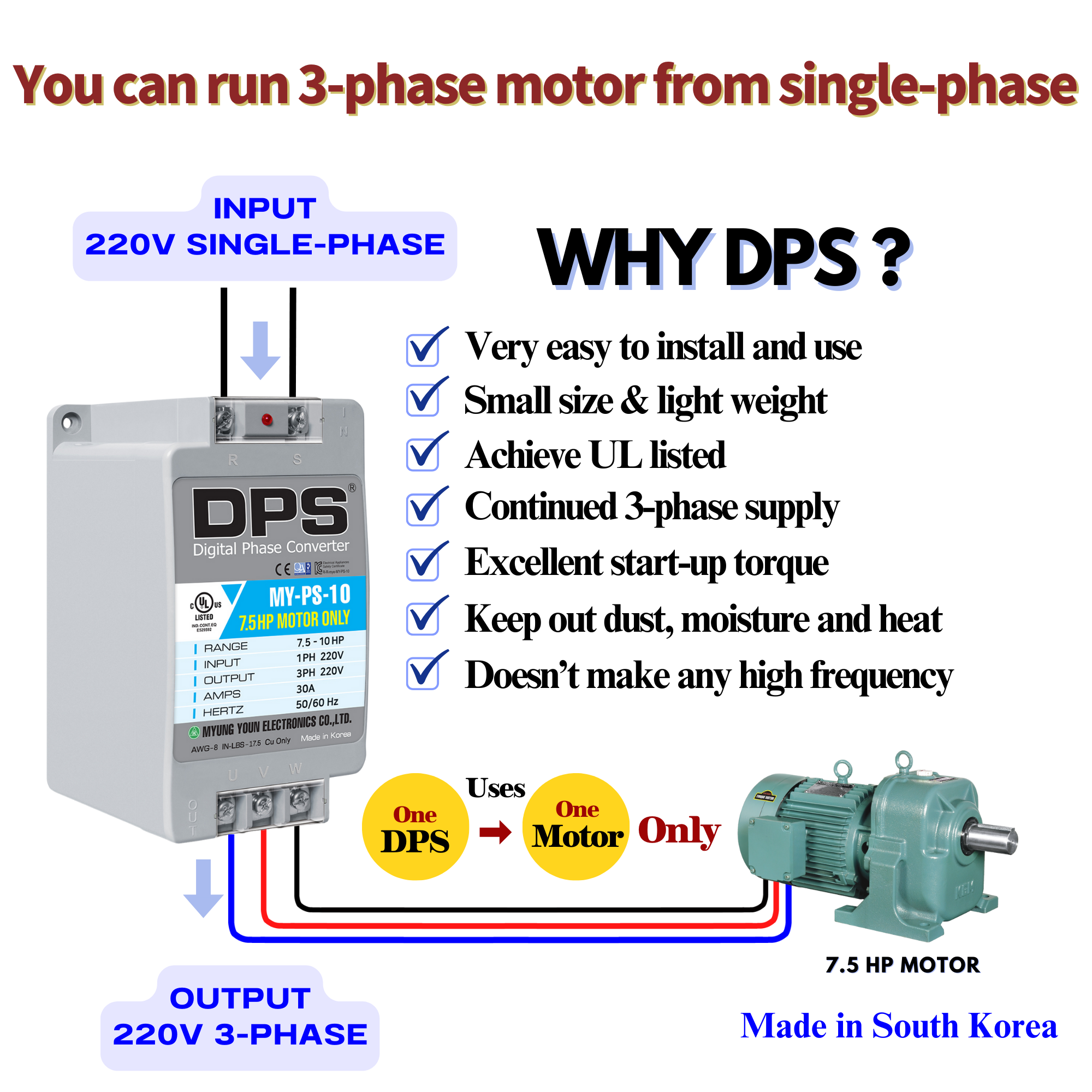
Three-phase power is a type of electrical power system where three alternating current (AC) waveforms are generated, each offset by 120 degrees. This configuration provides several advantages over single-phase power, including:
Increased power output: Three-phase systems can deliver significantly more power than single-phase systems of the same voltage and current.
While three-phase power is the preferred choice for many industrial applications, it is not always readily available. In rural areas or remote locations, single-phase power may be the only option. In such cases, a phase converter becomes essential to operate three-phase equipment.
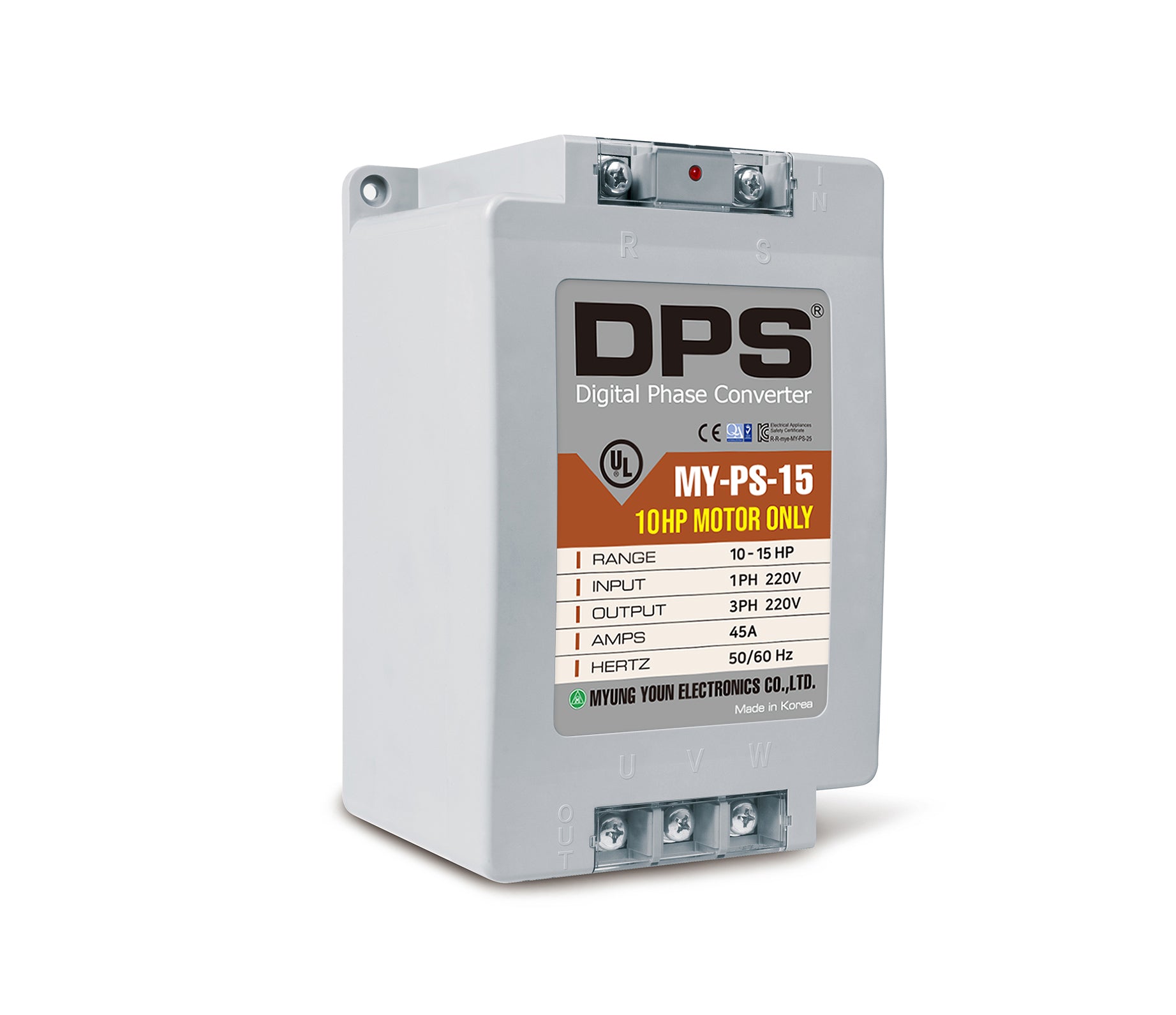
Before the advent of digital technology, rotary phase converters were the primary method for converting single-phase power to three-phase. These devices utilize a motor-generator set, where a single-phase motor drives a three-phase generator to produce the necessary output.
Size and Weight: Rotary phase converters are typically large and heavy, making them difficult to transport and install.
Digital phase converters have emerged as a superior alternative to traditional rotary models. They utilize advanced electronic components, such as power electronics and microprocessors, to generate the necessary three-phase waveforms.
Power Electronics: These components, such as Insulated Gate Bipolar Transistors (IGBTs) and MOSFETs, are responsible for switching the input power and creating the desired output waveforms.
1. Single-Phase Input: The digital phase converter receives single-phase power from the utility grid.
2. Waveform Generation: The microprocessor analyzes the input waveform and generates control signals for the power electronics.
3. Power Switching: The power electronics rapidly switch the input power, creating two additional phase voltages that are 120 degrees out of phase with the original input.
4. Three-Phase Output: The resulting three-phase output is then supplied to the connected three-phase equipment.
Compact Size and Weight: Digital phase converters are significantly smaller and lighter than rotary models, making them easier to install and transport.
Digital phase converters find widespread applications in various industries, including:
Manufacturing: Powering machine tools, conveyors, and other industrial equipment.
Choosing the appropriate digital phase converter depends on several factors, including:
Load Requirements: The size and type of three-phase equipment to be powered.
Integration with Smart Grid Technologies: Digital phase converters can be integrated with smart grid technologies to optimize energy consumption and improve grid stability.
Digital phase converters represent a significant advancement in power conversion technology. Their compact size, high efficiency, and quiet operation make them an attractive alternative to traditional rotary models. As technology continues to evolve, we can expect to see even more sophisticated and versatile digital phase converters in the future, enabling the reliable operation of three-phase equipment in a wide range of applications.
digital phase converter